It depends on the details
With new, smart suspension, powder coating specialist Proton Finishing Alsab has created world-class energy efficiency. All thanks to the great co-operation with local supplier HangOn.
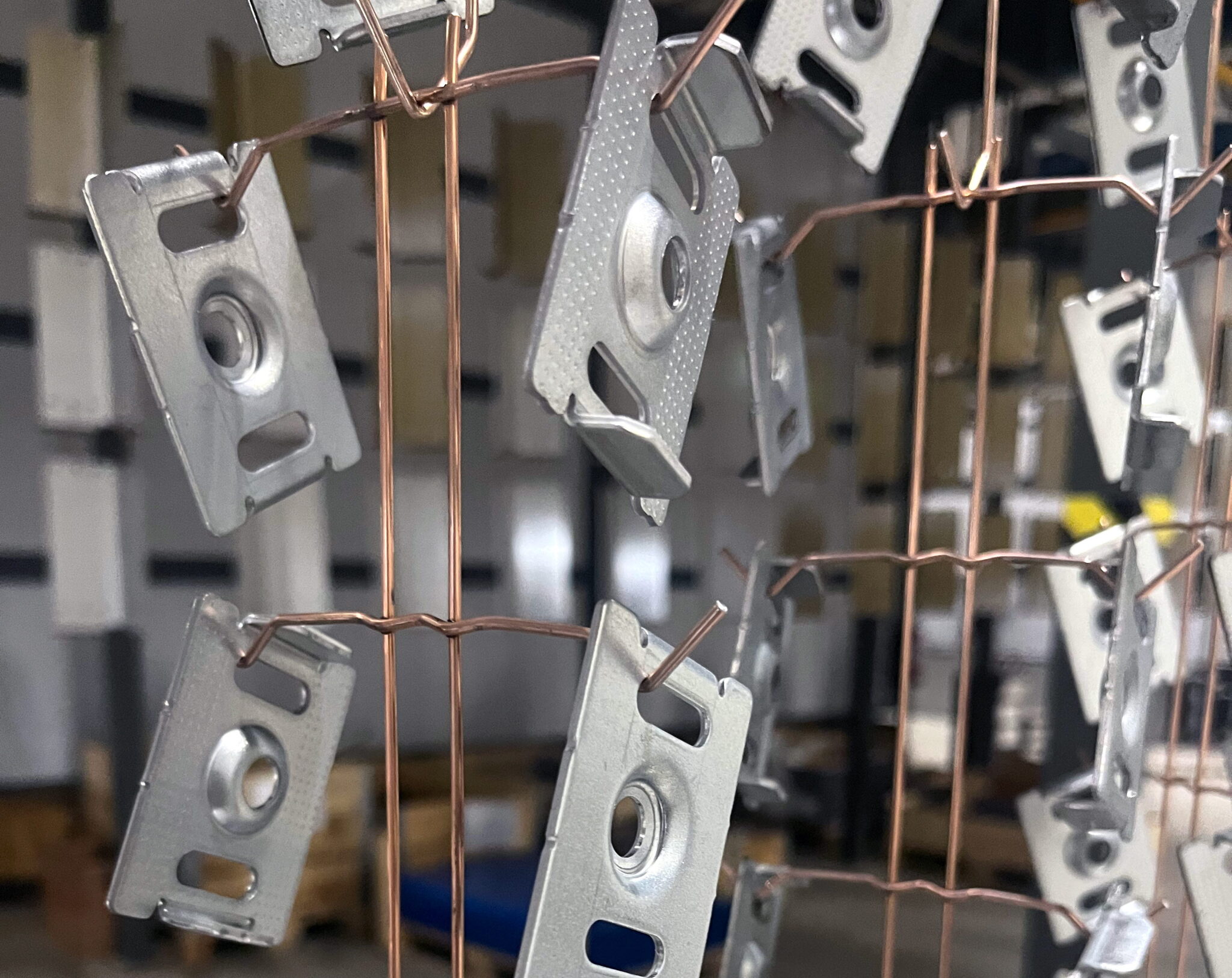
We already had a high level of energy efficiency in our operations.
In the context of the energy crisis, all of Proton Finishing’s units started to evaluate the possibilities of energy saving and further limiting the carbon footprint. Something that would prove to be a challenge at Proton Finishing’s unit in Anderstorp.
– ‘We already had a high level of energy efficiency in our operations,’ says Liam Tran.
However, the long-standing collaboration with HangOn sparked the idea of reviewing the hanging process itself. Maybe there was energy to be saved here?
– We have developed our own calculation programme, which we call HangOn Coating Calculation and which takes into account the entire powder coating process – not just the actual hanging. And it confirmed that there were great opportunities for efficiency improvements,’ says Jonas Törnquist.
Difficult to keep up
Before painting, all the details are hung on a fixture that then goes into the paint booth. At Proton Finishing, and almost all other powder coating companies, this work is done manually.
– ‘The opportunities for automation are, at the moment, very small in this industry because it often involves large variations and short series. You need to reach very large volumes for automated suspension to be an option,’ says Jonas.
At Proton Finishing Alsab, the paint line has a bottleneck that cannot be removed: there is simply a limited area where the actual suspension can be done.
– We simply cannot fit as many people as we want, which made it difficult to keep up with the line. In addition, the number of items that could be hung was limited by ergonomics. You can hang at face height plus half a metre up or down. The rest of the fixtures went into the paint booth empty,’ Liam explains.
Up to 90% energy savings
With more parts going into the paint booth, you also utilise the energy better, while the quality of the powder is even better because it doesn’t need to be recycled as many times,’ says Jonas.
energy savings
Ten times more details
The solution was HangOn’s new standardised hanging system HQW D. In this particular case, with a customised pitch and length to get the most out of the paint facility. The fixtures, which are one metre long, are pre-assembled elsewhere in the factory and then connected to form two-metre-long ‘curtains’. The fixtures are stored on specially designed trolleys which are then driven out to the line where they can be hung, quickly and easily.
The result?
– With the new hanging system, we can fit 500 parts per metre instead of the previous 50, because we can hang the parts more tightly and use the full height of the paint booth. Employees have much better ergonomics and no longer feel stressed because they can’t keep up,’ says Liam.
More cases
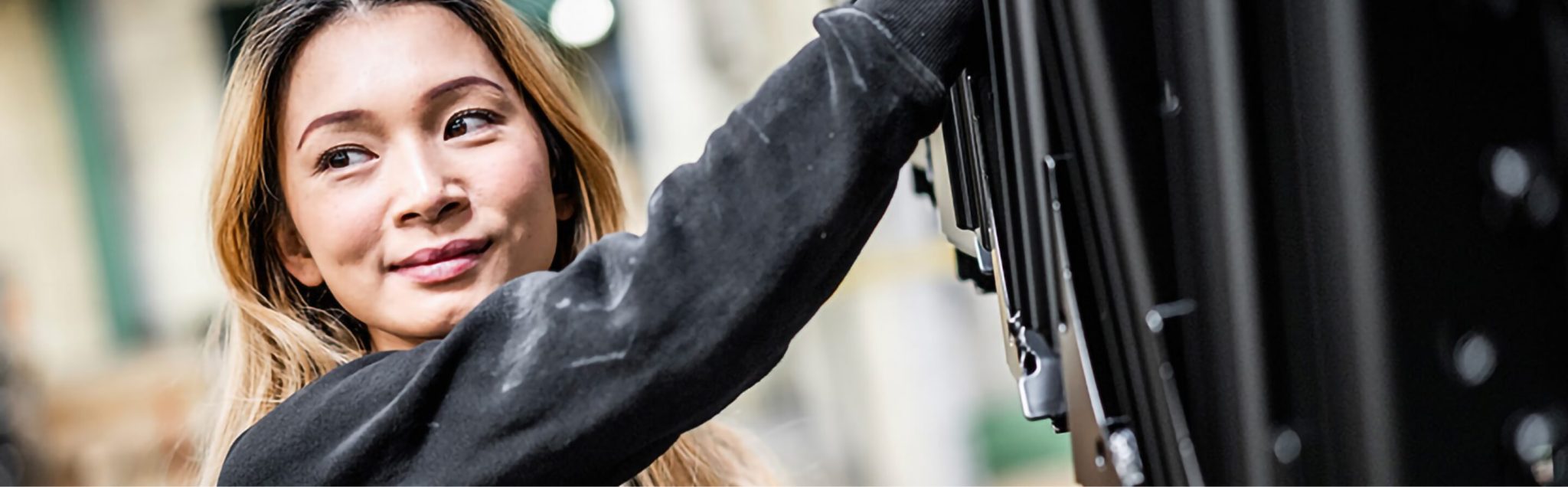