Safety brings social sustainability
Fazer is one of the largest food companies in the Nordic region and has a proactive safety programme. ‘This is a question of social sustainability,’ says Jonas Sundell, Health and Safety Manager at Fazer.
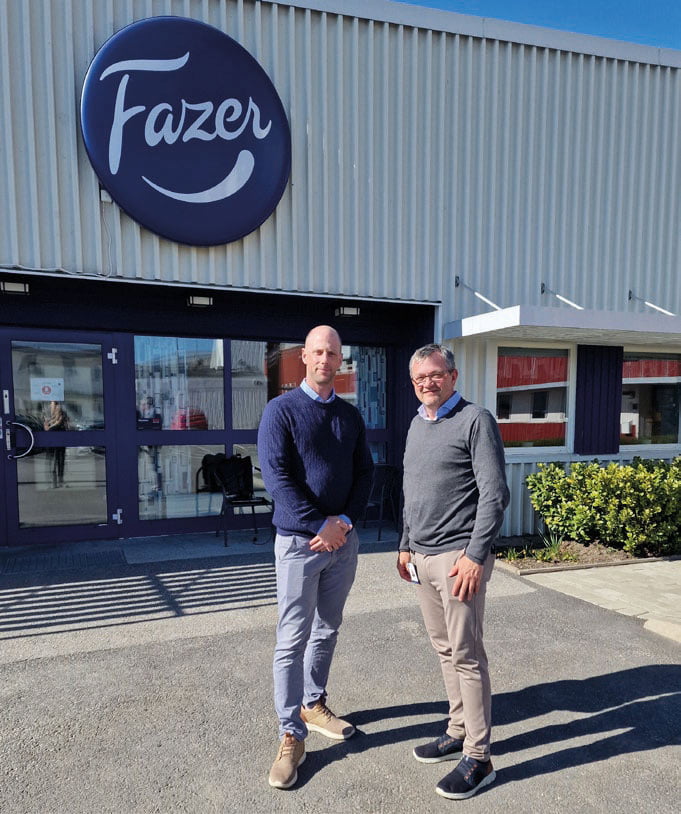
JL Safety a long-term partner of Fazer
The Machinery Directive sets out the essential health and safety requirements for all machinery placed on the market in the EU. Anyone involved in any type of machine-based production must ensure that they comply with the Machinery Directive. Not for its own sake, of course; the aim is to create safe workplaces where no accidents occur.
JL Safety in Skara, one of the companies in the Proton Edge business area, is a market leader in machine safety, risk assessments and CE marking. The company offers knowledge and tools for the regulations imposed on machinery and the use of work equipment, and helps customers with machine safety work – in its entirety or as needed.
One of the customers that has long collaborated with JL Safety to create a safe workplace is the food giant Fazer.
With a turnover of EUR 1.1 billion, Fazer is one of the largest food companies in the Nordic region and its products are exported to over 40 countries. Fazer’s operations in the bakery and confectionery, non-dairy and plant-based food markets are located in seven countries and employ a total of approximately 6,000 people. The three Swedish bakeries in Lidköping, Eskilstuna and Umeå employ around 500 people.
Action plan and risk assessment
– The collaboration with JL Safety began ten years ago when Fazer sought help to “sew up the bag” with all the elements of the Machinery Directive,’ says Dario Dzananovic, site manager at Fazer’s bakery in Lidköping.
Therefore, it was a natural choice to turn to JL Safety when Fazer launched the Safe Machinery 2025 project. A feasibility study led to an action plan where Fazer and JL Safety are now jointly reviewing procedures so that they are harmonised between the various bakeries. Strategic people are appointed and trained to increase competence in machine safety and CE marking, people in Fazer’s management, safety representatives, purchasing as well as maintenance and project management.
– We have carried out a machine inventory and continued to make risk assessments on all machines and machine lines. We have carried out these risk assessments both internally and with the help of JL Safety,’ says Jonas Sundell, who is the work environment manager at Fazer.
”Same condition or better”
Safe workplaces should be a given in all organisations. Yet Jonas Sundell was pleasantly surprised when he took up his position at Fazer three years ago.
– ‘I was impressed that safety is number one in the company. Fazer has made a central decision that all machines and machine lines that are part of the various bakeries should be at the forefront of safety, says Jonas.
‘It’s about minimising accidents and incidents with old, new and rebuilt machines. All of the 500 or so employees who work at Fazer’s bakeries must know what applies in terms of machine safety, hygiene and food requirements.
Dario, who is in his fifth year at Fazer, elaborates on the idea:
– You should go home in the same condition as you came to work, if not better. In fact, proactive safety work is seen as part of Fazer’s sustainability efforts.
– Absolutely, this is a question of social sustainability,’ says Jonas.
A labour that never ends
Complying with the Machinery Directive involves so much more than what appears at first glance to be purely safety issues,’ explains Dario. ‘You have to carry out skills upgrading, you also have to take stock of machinery and technical standards – and all the actions in a review bring improvements, not only for safety. Production staff, managers
– all of us together make risk assessments that result in better processes and greater sustainability. We even see benefits in reduced energy consumption in the long run,’ says Dario. It is clear from the conversation that he is very passionate about this.
– Every company says safety is number one, and many companies do very good things, but what I am proud of and can really vouch for is that the safety work here is not triggered by changes such as purchasing or other events.
Fazer’s safety efforts are budgeted for in a continuous plan, as are the risk assessments and training we carry out with JL Safety, using their Cedoc software,’ says Dario.
Collected experience
Fazer works with the LOTO safety concept, which is a procedure for safe access to machines, with locking procedures for operators and maintenance personnel.
– JL Safety provides support and helps us to develop this work. The staff are very knowledgeable and easy to reach, and the high availability is something we really appreciate,’ says Jonas. Dario continues: ‘JL Safety has helped us to coordinate everything, to work in a standardised and uniform way and to train us. It is a co-operation that works extremely well.
Dan Assarsson, Operations Manager at JL Safety and the person who has worked most closely with Fazer, describes the collaboration in equally positive terms: ‘It’s a big project that Fazer has taken on, to secure their facilities with risk assessments. We have worked with Fazer for many years and also with other players in the food industry. Now we have brought all that experience to create the best possible conditions for Fazer to have safe machines for its employees and thus create sustainability for everyone through decent working conditions. Sustainability and safety always go hand in hand, says Dan Assarsson.
More cases
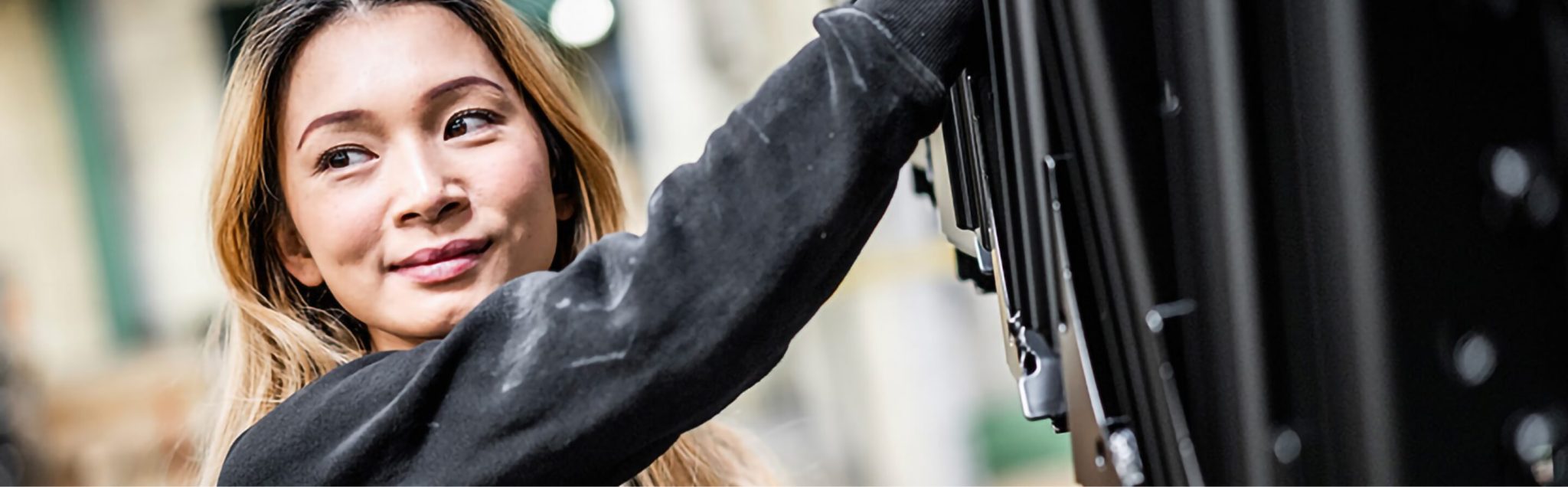