No pipe dream in the Port of Gothenburg
Tradition is silver, but innovation is gold. When Stena Oil in the Port of Gothenburg converted its oil tank, it chose to break new ground with an innovative heating technology from BRUGG. The project required extensive collaboration with several specialists. Weldin Gothenburg is one of them.
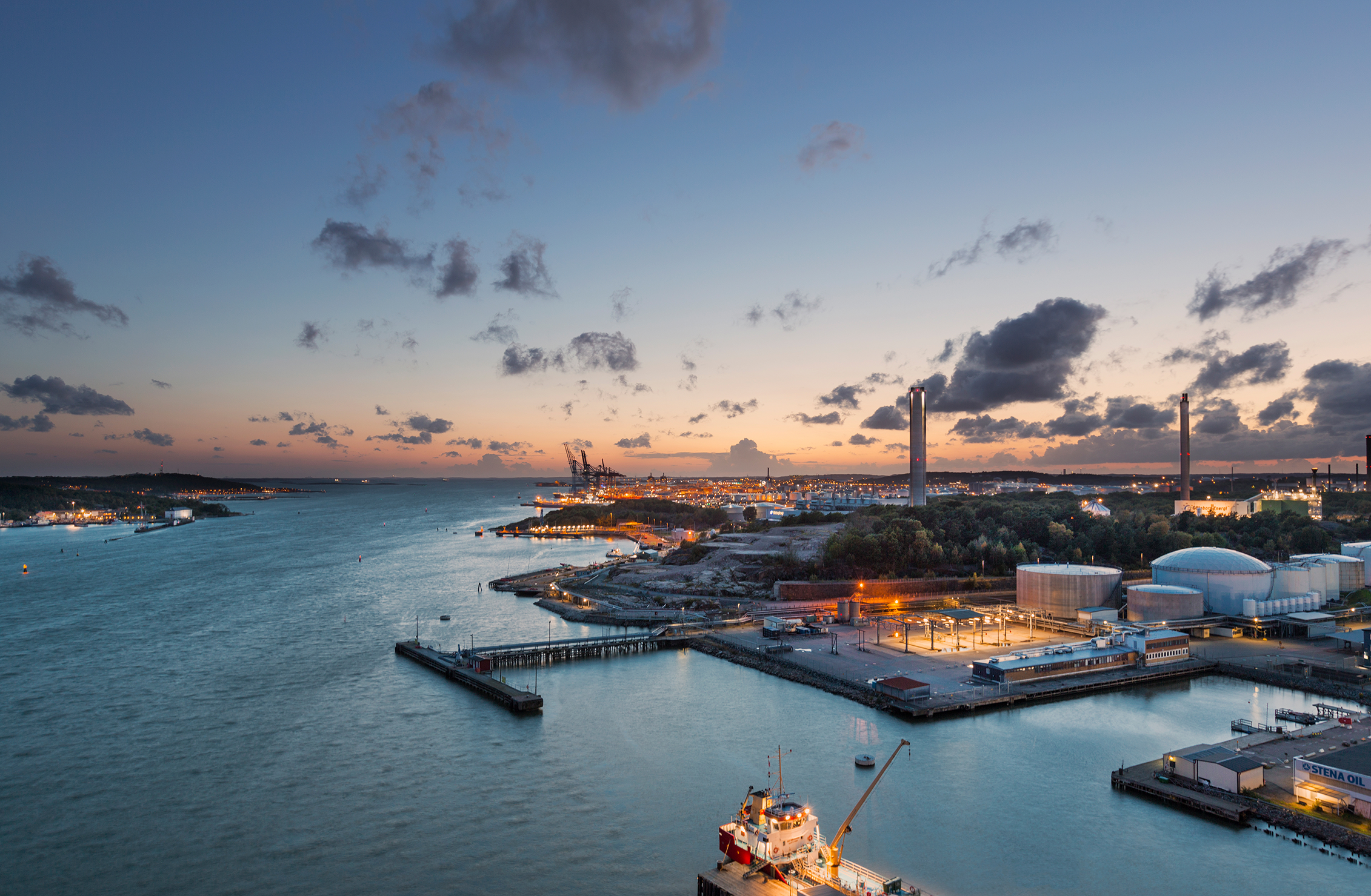
The Port of Gothenburg is Scandinavia’s biggest, and the gateway to the world for Swedish industry. Ships from every corner of the world load and unload goods here, and they also need to replenish their fuel oil, lubricants and other petroleum products. Refuelling a cargo ship is called bunkering. In the Port of Gothenburg, Stena Oil is responsible for ensuring that vessels can continue on their way.
Knivigt att göra rent
“We store oil and other fuel in cisterns in the port,” says Martin Josefsson, head of security at Stena Oil.
“We fill up our own bunker ships from these tanks and sail out to bunker up the customers’ ships.” Recently, Stena Oil acquired a cistern from its sister company Stena Recycling, which has a neighbouring facility.
“There’s precious little space in the port, so when we got the opportunity to take over one of their existing tanks it was a perfect solution.”
The 10,000 m3 tank – considered medium-sized in the industry – is a welcome addition to our storage capacity, which is about 100,000 m3.” But first the tank needed to be fitted with heating coils.
“We need heat to minimise the viscosity of oils or biomass, which is a bit thicker,” Martin explains.
“Normally we weld in an extensive pipe system weaving over the whole base of the tank. The problem with the traditional solution is that it’s difficult to clean the tank after emptying it. You go in manually and clean it out with big rubber scrapers, which is quite difficult with criss-crossing pipes.”
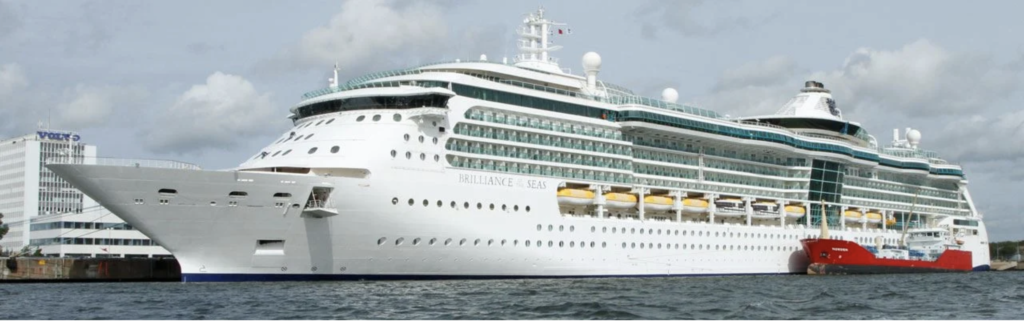
Innovative installation
Stena Oil chose the specialist BRUGG Pipes to do the remodel, and they suggested a completely new type of pipe system for heating. The Swiss company specialises in manufacturing and selling pipe systems for safe, efficient transport of industrial fluids and gases. They have become well-known for short installation times and downtimes thanks to a large degree of prefabrication. Their Swedish subsidiary BRUGG Sweden designs complete solutions from consulting and planning to project management and implementation.
“We suggested a completely new solution for Stena Oil, based on two concepts: the Norflex heat exchanger pipe, which is made of acid-fast steel, and the Bioflex pipe, which is made of stainless steel,” says Daniel Olsson, Chief Operating Officer at BRUGG Sweden.
“The point of our systems is that they have spiral corrugation, which facilitates the use of screws and couplings. This means longer pipe lengths and fewer joints, and above all greater flexibility, so you can install them in a cleverer way, along the tank walls where they aren’t in the way as much and at the same time provide a greater surface for heat transfer, making the system more effective.” The result is that Stena Oil will have more efficient heating of the tank and will save many man-hours on cleaning, not to mention the more convenient installation.
Cutting edge technology
As a sales company, BRUGG does not have installers in Sweden. Rather, they have chosen to use selected local partners to offer a complete package in the project. Rördesign AB was responsible for the pipe structures and Proton company Weldin Gothenburg (former GH Svetsteknik) installed the heat exchanger package with its steel structures.
“For us on the Swedish market, this is a new pipe system. As far as we know, this type of installation has never been done in these contexts before,” says Gunnar Hansson at Weldin Gothenburg.
“That made the project extra exciting; it’s a privilege to have been involved in such a complex project that requires so much collaboration and dedication from all parties.” Gunnar and his crew are not at all bothered that the new solution with longer pipes and simpler installations actually means less welding and thus less work for them.
“Absolutely not! Considering all the steel structures that still have to be built, a project like this will still mean plenty of work. Besides, we want to lead the charge for new solutions and develop leading-edge technology in the industry, so it’s fantastic to have this opportunity to innovate with colleagues. No one benefits from hanging on to outdated methods.”
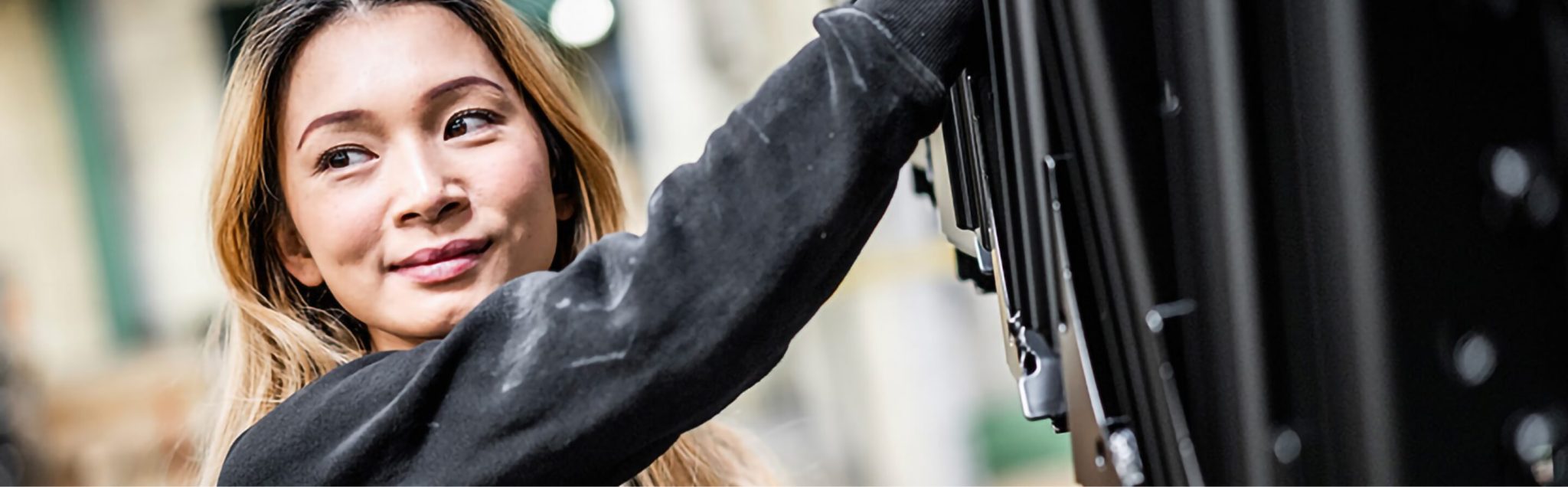